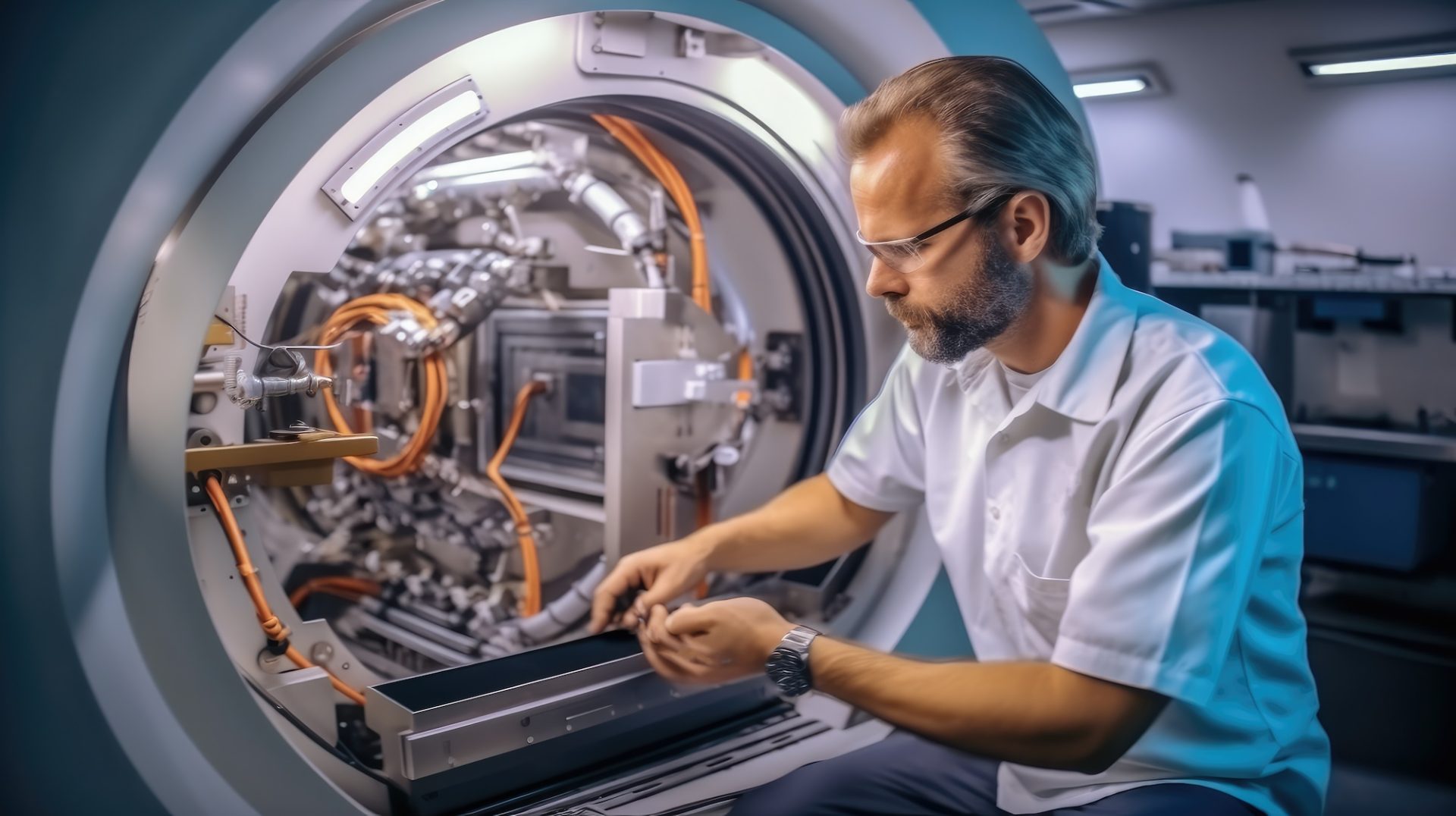
Minimizing Downtime
Background
Downtime in manufacturing can lead to significant financial loss. When a customer’s plant faced an unexpected line shutdown due to a 125HP drive failure, the stakes were high. The local distributor team was initially contacted but found no replacement drive available within their network or in the manufacturer’s inventory.
Challenge
The plant was on the brink of a prolonged downtime, with the only immediate alternative being a repair that would take at least 3-5 days. This situation posed a significant challenge as the plant was losing approximately $15,000 per hour in production.
VANTAGE’s Intervention
VANTAGE Electrical Group leveraged its comprehensive data capabilities to identify potential solutions. Utilizing historical purchase data, VANTAGE pinpointed six drives of the same frame size that had been previously purchased and might be suitable replacements.
Solution Process
- Data-Driven Identification: The VG SAM (Strategic Account Manager) utilized manufacturer software to assess compatibility differences among the six identified drives.
- Optimal Drive Selection: One of the drives was found to be compatible with the failed unit, requiring only minor modifications to function.
- Resource Optimization: The drive was located at another customer’s site, where it was confirmed to be a spare and not in use.
- Rapid Deployment: Necessary modifications were communicated, and the drive was quickly dispatched to the site experiencing the downtime.
Overcoming System Limitations
The customer facing the downtime was unable to locate the spare drive due to discrepancies across three different ERP systems they operated. The plant in need was searching for an exact part number, which hindered their ability to find a suitable replacement quickly. Vantage’s ability to cross-reference data across different systems was crucial in identifying and procuring the spare drive.
Outcome
By deploying the spare drive swiftly, VANTAGE helped the plant resume production significantly faster than if they had waited for a repair. The quick turnaround prevented a potential loss of approximately $1,080,000 over an estimated downtime of 72 hours.
Conclusion
This case study highlights the value of VANTAGE Electrical Group’s data-driven approach in managing emergencies and reducing production downtime. VANTAGE’s effective use of comprehensive data and strategic asset management capabilities not only saved the customer significant financial resources but also demonstrated the potential of integrated data systems in solving critical operational challenges.